The
uniaxial test
The uniaxial test describes the mechanical behavior
of a material when loaded along a single direction. These tests
are usually performed on a universal testing machine machine. For
very high strain rate tensile tests (useful for impact analyses),
an inexpensive solution is currently in development at Datapoint
Testing Services, using a Dynatup impact tester.
The resulting stress-strain curves are very different
for metals and polymers (Figure 1). For metals the behavior is linear
within a very small range corresponding to the elastic response
of the material. The elastic limit, or yield point, is usually defined
as the point where the linear prediction deviates from the actual
curve by 0.2% (called the 0.2% offset point). At larger strains,
plastic flow occurs and the curve becomes non-linear. Most of the
plastic deformation occurs by slip within the crystalline structure
of the metal. At the ultimate stress, the specimen breaks.
Figure 1. Typical stress-strain curves
for aluminum and polystyrene.
The stress-strain curve of a typical polymer
is very different from metallic materials. The elastic region is
wider than for metals but nonlinear. The yield point is therefore
more difficult to find and requires special experimental procedures:
the specimen is loaded and unloaded, increasing the load at each
cycle until a permanent deformation is observed. That point is then
taken as the yield point. For larger strains, plastic deformations
occur by homogeneous viscoplastic flow, shear bands or formation
of crazes at the surface of the specimen.
Compression versus tension
For metals, compressive and tensile deformations
imply the same mechanism and the stress-strain curves are consequently
similar (same elastic moduli and yield strengths when the material
has no plastic loading history). To analyze a metallic part experiencing
multiaxial loads, a stress strain curve in either tension or compression
is sufficient. For investigations on plasticity in tri-dimensional
analyses, the Von Mises yield surface is widely used and gives excellent
results. This criterion can be written as:
Where ó is the equivalent Von Mises stress
and óy is the yield stress obtained with a stress-strain
curve.
For polymers, the symmetry of the stressstrain curve is not observed.
Elastic and plastic deformations of polymers are sensitive to the
hydrostatic pressure. These deformations imply entanglement of the
molecules, and this mechanism is slowed under high pressures, as
the molecules are compressed against each other. The immediate consequence
is that the response in tension and compression is different: in
compression (for high hydrostatic pressures), the material is generally
stiffer and has a higher yield strength than in tension. A modified
yield surface (Figure 2) should be used:
Where P is the hydrostatic pressure and a is
a constant. In addition to this effect, tensile deformations result
in the formation of crazes at the surface of the specimen. Crazes
are crack-like deformations which reduce considerably the strength
of the material in tension (see stress-strain curve for polystyrene).
Very often a structural parts endures both compressive and tensile
stresses. In contrast to metals, the designer should use data in
both tension and compression to obtain more realistic results.
Strain rate and temperature effects
When modeling a material, strain rate effects
are taken in account when the temperature reaches typically one
half of the melting temperature (viscoelastic and creep effects),
or for high strain rates (damping in vibration analyses). For metals
under low temperatures and quasi-static loads, the strain rate effect
can be neglected.
For polymers, these effects cannot be ignored: due to their low
melting temperature, rate dependencies are much more pronounced.
Indeed, the non-linearity of the elastic region can be in part explained
by the viscosity of the polymer. High strain rates lead to higher
stresses within the specimen. Moreover, the viscosity of the material
is very sensitive to the temperature. Decreasing the temperature
increases the viscosity, and therefore increases the stresses. A
successful analysis should therefore be performed using data obtained
at strain rates and temperatures close to the actual loading conditions
of the structural component.
Principles of Polymer Engineering, 2nd Edition
N. G. McCrum, C. P. Bucknall, C. B.
Bucknall. Oxford Science Publications, 1997. ISBN 0-19-856526-7.
Reviewed by Hubert Lobo.
This book presents a concise and easily readable
introduction to polymer behavior for design and production engineers.
It seeks to explain the behavior of plastics and rubber using a
materials science framework, by relating observed phenomena to changes
in morphological and molecular structure. This presents a powerful
way for engineers to grasp the underlying factors that make polymers
the complex materials that they are. The reader is encouraged to
step away from using linear-elastic metals concepts when designing
with plastics. The pitfalls of such simplifications are pointed
out and guidelines are presented to aid the designer in adopting
a non-linear approach.
Numerous examples throughout the book illustrate how these concepts
may be applied. Chapter 2 provides an introduction to the structure
of a polymer, and to the phenomena of melting, solidification and
orientation, which play such important roles in defining the morphology
and performance of a polymeric component. This puts the reader in
the right frame to examine the behavior of rubber, which is covered
in the next chapter. Here, the implications of large deformation
are considered while important distinctions between polymeric and
metal behavior are made. The issue of viscoelasticity is covered
next, along with its implications in the prediction of creep and
stress relaxation. The treatment of this complex subject is easy
to follow and is accompanied by well-developed insights, which make
it possible for the engineer to apply these concepts to everyday
design.
In Chapter 5, we see a presentation of the mechanisms of failure
in plastics and rubber. This chapter has been extensively updated
to reflect the new developments in this field. Yielding and necking
phenomena are explained along with descriptions of brittle failure.
The effects of fiber fillers, rubber as toughening agent and other
reinforcements are covered.
The remainder of the book is devoted to the processing of polymers.
Each of the major manufacturing processes is treated using the same
framework. The last chapter is of particular interest to design
engineers. Issues of material selection, the choice of processing
technology and its effect on performance are considered. The sections
on designing for stiffness and strength provide guidelines on the
effect of different variables on the performance of a polymeric
part.
Increased demand for services drives major
expansion
In response to the growing need for accurate
material data for design, Datapoint Testing Services has acquired
additional laboratory and office space, added an engineer and two
test technicians to its staff, and
purchased additional test equipment.
New personnel
François Barthelat has joined Datapoint
Testing Services in the position of Applications Support Engineer.
François, who holds an M.S. degree in mechanical engineering
from the University of Rochester, brings expertise in performing
structural analysis. Datapoint Testing Services also welcomes Brigitte
Nassar and Gregory Urbancik, who join our staff as Laboratory Technicians.
Brigitte holds a diploma in Theoretical and Applied Physics from
the University of Heidelberg; Greg graduated from the College of
New Jersey with a B.S. in Biology.
New equipment and test offerings
Datapoint Testing Services has purchased a Satec
fatigue tester, used to determine the number of cycles to failure
as a function of stress. The fatigue tester has been outfitted to
perform measurements at elevated temperatures. A moisture analyzer,
a surface tension measurer, a compression set fixture, and an optical
stage for microscopic determination of transition temperatures have
also been acquired.
Course introduces properties for FEA
Datapoint Testing Services and MARC Analysis
Research Corporation are currently developing a material properties
course for designers and engineers in the plastics industry. The
two-day course, to be held on the West Coast at the end of this
summer, will combine lectures and hands-on experience. Attendees
will perform mechanical tests and use the resulting data for simulations
with MARC software. For details, contact Gary Timpe at 206-729-5740.
Lab passes 2000th material milestone
As of February of this year, Datapoint Testing
Services has performed mea surements on more than two thousand materials.
TestPaks® for MSC/ NASTRAN,
MARC are offered
Datapoint Testing Services has expanded its structural
analysis test offerings by creating TestPaks® for
MARC and MSC/NASTRAN. Each TestPak® contains all
the measurements required to characterize a material according to
a particular material model. The resulting data is supplied both
in a written report and electronically, ready to load into the structural
analysis package. TestPaks® for MARC and MSC/ NASTRAN
range from simple linear material models to more complex non-linear
models, including hyperelastic models. Effects of temperature and
rate-dependency can be included, and creep and viscoelastic effects
can also be characterized.
With the addition of MARC and NASTRAN, Datapoint Testing Services
now provides TestPaks® for 17 of the most widely
used FEA software packages in the world today.
A2LA accreditation achieved
A2LA has accredited Datapoint Testing Services
to ISO/IEC Guide 25 for technical competence in the field of mechanical
testing. Our scope of accreditation also encompasses many thermal
properties, including capillary rheology and thermal conductivity.
For additional information regarding accreditation, contact our
Laboratory Manager.
A2LA accreditation ensures laboratory competence
For a laboratory to be accredited by A2LA (American
Association for Laboratory Accreditation) it must meet all of the
requirements of ISO/IEC Guide 25, “General Requirements for
the Competence of Calibration and Testing Laboratories”. To
accomplish this, the laboratory must show that it complies with
the quality system requirements of ISO 9002 (Quality Systems: Model
for Quality Assurance) and it must demonstrate that it and its staff
are competent in the tests which appear on its scope of accreditation.
This is no small feat. In order to be accredited by A2LA the laboratory
must submit a laboratory quality manual describing the operation
of its quality system. It must also have written test methods, policies
and procedures for document control; procedures for achieving traceability
of measurements; calibration, verification, and maintenance procedures
and schedules; and procedures for audit and review of the entire
quality system in the laboratory. (This list of requirements is
not all-inclusive.) Before the laboratory can be accredited it must
undergo a rigorous in house assessment by an auditor with knowledge
of quality system requirements and expertise in the field of testing
for which expertise is sought. Laboratory staff members must demonstrate
to the assessor their competence to run and understand all methods
for which the laboratory claims they are qualified. Any deficiencies
found during this assessment must be satisfactorily resolved before
accreditation is granted.
So what does this mean to anyone serviced
by this accredited laboratory?
Working with an A2LA accredited laboratory provides to the client
confidence that the lab equipment is properly calibrated and maintained,
and that those who run the tests are trained, competent, and qualified.
The client can be assured that the test results provided are reliable
and accurate. The client can have confidence in the operation of
the laboratory without having to perform its own on site audit.
Competence is the key word in accreditation to ISO/IEC Guide 25.
This means that the laboratory has demonstrated that it has in place
a quality systems program and that it performs tests both consistently
and correctly, thus providing confidence to the client that the
test results are accurate.
Paul Graboff is an independent plastics consultant based in Augusta,
GA. He holds a BA and an MS in Chemistry, and has over 40 years
experience in testing, quality assurance, and standardization.
Upcoming events
ANTEC’99:
Plastics–Bridging the Millenia. Meet Hubert Lobo and Gary
Timpe at our booth. May 2 - 6, New York, NY.
ABAQUS User’s Conference.
May 26-28, Chester, UK.
1999 ICCON User’s Conference.
June 14-18, Anaheim, CA.
1st Worldwide MSC Automotive User’s
Conference. Sept. 20 - 22, Munich, Germany.
|
|
Figure
2. Yield surfaces predicted by the Von Mises criterion, with hydrostatic
pressure dependence correction and with crazing effects.
Figure
3. Stress-strain curves obtained at different strain rates and temperatures.
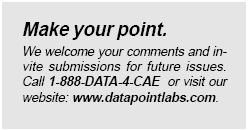
|