|
Finally, getting this behavior into the analysis usually requires
a material model. The hyperelastic material models present a number
of options to aid in a best fit of the material data. The Mooney-Rivlin
model is by far, the most common model in use today. It presents
many advantages in terms of being able to handle the different kinds
of behavior seen in rubbers. The ability to increase the number
of modes permits the handling of large strain behaviors with some
level of dexterity. The objective of any model development effort,
however, is to fit the data at as low a number of modes as possible.
As stated above, an important guideline in model fitting is advance
knowledge of the strain range of interest. The Ogden model also
offers great versatility in fitting the complex behavior of rubber.
The choice between these models is often governed by the goodness
of fit to the actual data. However, as pointed out by Boyce [1],
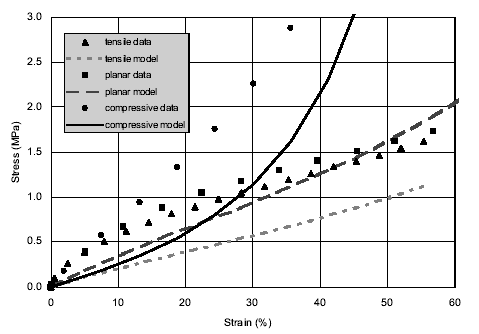
Figure 2. Arruda-Boyce model
is unable to fit non precycled rubber
these empirical models may not be as robust as those based on statistical
mechanics. The more recent Arruda-Boyce model is a promising model
that has a statistical mechanics basis. This model presupposes a
certain kind of rubber behavior so that it has the capability to
work well for materials that obey its laws. A big advantage of this
approach is that the model can then predict behavior in multiple
modes from data taken in only one mode: tension. We find in our
work, however, that there are some materials that do not obey its
laws so that the need for more detailed characterizations cannot
be eliminated. Additionally, the Arruda-Boyce model does not handle
the initial deflection region well, rendering it not as useful for
small deformation modeling of rubbers. In comparison, the Mooney-
Rivlin model does a better job because it has the potential of a
greater number of coefficients and is able to handle such behavior.
Further, we observed that the Arruda-Boyce model has difficulty
with biaxial (compressive) data [2].
Careful consideration to the needs of a particular simulation can
yield considerable benefits when modeling rubber materials.
References
[1] M.C. Boyce and E.M. Arruda, J. Rubber Chem. Tech v.73, pp 504-523
(2000)
[2] D.J. Siebert and N. Schoche, J. Rubber Chem. Tech, v.73 pp 366-384
(2000)
DatapointLabs unveils new e-commerce enabled web-site
Figure 1. New home page of DatapointLabs.com
ITHACA, NY: May 7, 2001-DatapointLabs launches its new e-commerce
site www.datapointlabs.com
to lead the industry as the first web-enabled materials testing
company. The new web site offers all the information a user needs
to make an easy online purchase, and serves as a resource for over
150 tests used for research and development, product design, automotive
certification and quality control. It allows users control of their
orders and past orders history. "We are trying to provide a
virtual expert on-line, ready to guide our users to select the tests
that best meet their material testing needs. Of course, our laboratory
staff is always here to assist the user,"
states Hubert Lobo, President.
TestPaks® Alliance
Program
The new site also gives greater exposure to DatapointLabs? TestPaks®
Alliance Partners. Here, users can view details about CAE programs
supported by DatapointLabs. TestPaks® for each program
are conveniently categorized permitting CAE analysts to select the
material models they need. Guidance is provided on the use of the
material models that are supported.
Dale Hummel named CRM Manager; new
personnel added
Dale Hummel has been appointed Customer Relations Manager. Customer
relations becomes crucial in the new Internet economy when people
rely on the impersonal world- wide-web to communicate and transfer
information. "We are fortunate to have such an experienced
manager to take up this role at DatapointLabs, In conjunction with
his current role of Operations Manager, Dale is the eyes and ears
of the customer in the laboratory" says Hubert Lobo, company
president. Kelly Evans, a recent graduate from Ithaca College has
joined DatapointLabs as an Administrative/ Sales Associate. Kelly
is a published writer and an avid softball player.
New Tests
Low Temperature Bend Test- ASTM D2136
Fabrics coated with rubber or rubber-like materials display increased
stiffening when exposed to low temperatures. This test describes
a pass/fail procedure by which material flexibility at a specified
low temperatures can be determined.
HDT(ASTM D648) & VIcat (ASTM
D1525)
This classic bend test measures the temperature where a specified
flexural load cannot be sustained by the material. The Vicat test
is similar but uses a point stress instead.
Expanded ISO Test List
The following ISO tests have been added to the on-line catalog.
ISO 527-1
Tensile tests
ISO 604
Compressive tests
ISO 178
Flexural tests
ISO 180 Izod
impact tests
ISO 179
Charpy impact tests
ISO 6603-2
Instrumented impact tests
ISO 899
Creep tests
ISO 75-1
Heat deflection temperature
ISO 11357
DSC
ISO 1183
Density
Upcoming events
ABAQUS User's Conference.
May 30-June 1, Maastricht, The Netherlands.
FIDAP and Polyflow User's Group Meeting.
June 19, Skokie, IL.
ISO TC61 Meeting.
September 9-15, Berlin, Germany.
Moldflow 2001 Internaltional User
Group Meeting. September 17-19, Boston,
MA.
Articles discuss use of engineering
properties in simulation
Plastics researchers, CAE analysts, processors and producers gathered
at the Dallas Convention Center May 7-11 to attend the ANTEC 2001
conference and exhibition which showcased the latest developments
in the plastics industry. Of almost 1000 papers presented, we list
below our pick of noteworthy papers.
We noted a dramatic increase in the use of full 3D for injection
molding and extrusion CAE. Advances were seen for rotational molding
simulation. Significant progress was reported in the understanding
of crystallization phenomena. Novel work on finite element analysis
for impact and puncture simulation was also presented.
Injection molding
Modeling the Melting Process of Polymer Pellets Caused by Friction
(91), Yung, K.L., Xu, Yan, and Lau, Francis.
The Effect of Inertia on Fill Pattern in Injection Molding (739),
Costa, Franco S., Ray, Shishir, Friedl, Chris, Cook, Peter S., and
Xu, Shoudong.
Prediction of the Impact Behavior of Injection Molded Plates (82),Viana,
J.C., Cunha, A.M. and Billon, N.
Numerical Simulation of Injection Molding of Semicrystalline Thermoplastics
(633), Guo, Jianxin and Narh, Kwabena A.
A Novel Three-Dimensional Analysis of Polymer Injection Molding
(740), Chang, Rong-Yeu and Yang, Wen-Hsien.
Structure Performance of Thin-Wall Injection Molded Parts (77),
Chen, S.C., Jong, W.R., Chang, Y.P., Kang, Y., Peng, H.S., Huang,
L.T., Yang, L.K., Chang, C. T., and Luo, R.C.
3D Solid Brick Element Injection Molding Simulation-A Time Effective
Solution (44), Berhardt, Anne, Bertacchi, Giorgio, and Moroni, Antonino.
Analysis of Internal Structure of Injection-Molded Parts Based on
a Three-Dimensional Simulation Software (343),
Hoffmann, S. and Michaeli, W.
New Solidification Models for the Simulation of the Injection Molding
Process (592), Moneke, Martin, Amberg, Joachim, Bastian, Martin
and Alig, Ingo.
Full 3-D Prediction of Warpage of Injection Molded Parts (279),
Inoue, Y., Imai, K., Takahara, M., Murayama, Y., Matsuoka, T., Shinoda,
K., and Mori, Y.
Three-Dimensional Simulation of Injection-Compression Molding of
a Compact Disk (736), Chang, Rong-Yeu, Chang, Wen-Ya, Yang, Wen-Hsien,
Yang, Wen-Li, and Hsu, David C.
Three-Dimensional Modeling of Gas-Assisted Injection Molding (733),
Chang, Rong-Yeu and Yang, Wen-Hsien
Experimental and Numerical Analysis of Thin-Wall Injection Molding
with Micro-Features (718), Yu, Liyong, Koh, Chee Guan, Koelling,
Kurt W., Lee, L., James, and Madou, Marc J.
Rotational Molding
Non-Isothermal Melt Densification in Rotational Molding (787), Tiang,
J.S. and Bellehumeur, C.T.
Extrusion
Flow Analysis in Single Screw Extruders (177), Lawal, Adeniyi and
Railkar, Sudhir.
Three-Dimensional Numerical Analysis of the Single Screw Plasticating
Extrusion Process (735), Chang, Rong-Yeu, Hsu, Che- Wei, Yang, Wen-Hsien,
Yang, Wen-Li, and Hsu, David C.
Blow Molding
Thermomechanical Modeling, Microstructure Development and Part Performance
in Stretch Blow Molding (117), Laroche, D., DiRaddo, R., and Brace,
J.
Large Part Blow Molding (LPBM) of HDPE Resins: Parison Extrusion
Behavior and Its Relationship with the Resins: Rheological Parameters
(371), Jivraj, N., Sehanobish, K., Ramanathan, R., Garcia-Rejon,
A., and Carmel, M.
Thermoforming
Modeling of the Effect of Slip in Plug-Assisted Thermoforming (94),
Laroche, D., Collins, P., and Martin, P.
Robust Simulation for the Heating Stage in Thermoforming (114),
Yousefi, A., Bendada, A., and DiRaddo, R.
Experimental Investigation of Slip in Plug-Assisted Thermoforming
(630), Collins, P., Martin, P., Harkin-Jones, E., and Laroche, Denis.
Viscoelastic Material Characterization at Large Deformation (392),Kouba,
Karel, Novotny, Petr, and Kech, Armin.
FEA/Impact Simulation
Simulation of the Puncture Resistance of a Thermoformed Syringe
Pack (879), Christopherson, Roy and Briere, Marc.
Kinematics of Quasistatic Inflation of a Catheter Balloon Made of
Elastomeric Material: Simulation and Experiment (124), Guo, Xiaoping
and Bednarek, Michael.
Measurement of Strain Rate-Dependent Material Properties for Polymers
(713), Keuerleber, M., Eyerer, P., and Buhring, J.
Experimental and Analytical Verification of Plastics Material Models
for Automotive Crashworthiness Applications (597), Pitrof, Stephen
M. and Lee, Michael C.
Plastic Material Modeling for Vehicle Crash Simulation Using LS-DYNA
(897), Xiao, Xinran Sharon.
Failure Analysis of High Density Polyethylene in Engineering Applications
(352), Zhou, Wen and Chudnovsky, Alexander.
Material Characterization
The Role of Melt Dynamics in Shear-Enhanced Crystallization of Isotactic
Polypropylene (841), Oberhauser, James
P., Thurman, Derek W., and Kornfield, Julie.
Application of the Time Temperature Shift Principle to the Material
Behavior of Rubber under High Deformations (330), Grambow, Andreas
and Haberstroh, Edmund.
Measuring the Nonlinear Viscoelastic Material Properties of Thermoplastic
Materials by DMA (492), Schroder, O. and Schmachtenberg, E.
Friction Properties of Thermoplastics in Injection Moulding (25),
Ferreira, E.C., Neves, N.M., Muschalle, R., Pouzada, A.S.
Bulk Moduli from Enthalpy and Volume Data Obtained During Physical
Aging Experiments (684), Slobodian, P., Pelisek, B., Kubat, J.,
and Saha, P.
An Advanced (HMG) Short Glass-Fiber Reinforced Nylon 6: Part II
Mechanical Performance (1055), Kagan, Val A., McPherson, Rowena,
and Chung, Jerry S.
Reinforced Plastic Design: Tensile Versus Flexural Fatigue (455),
Krohn, John A., Novak, Glen E., and Wyzgoski, Michael G.
A Model and Parameter Formulation of Stress-Induced Crystallization
Kinetics of Polymers (634),Guo, Jianxin and Narh, Kwabena A.
Modeling Structural Recovery: Analysis of the Peak Shift Method(1039),Zheng,
Yong, Simon, Sindee L., and McKenna, Gregory B.
Extensional Flow Properties from Entrance Pressure Measurements
Using Zero Length Die Versus Bagley Correction (196),Sunder, J.
and Goettfert, A.
Flow Instabilities of Several Linear Polyethylenes in Capillary
Experiments and Effect of Die Materials (521), Larrazabal, Hector
J. and Hrymak, Andrew N.
Three-Dimensional Non-Isothermal Numerical Analysis of Multi-Layer
Coextrusion (732), Chang, Rong-Yeu, Ke,
Chao-Sheng, Yang, Wen-Hsien, Yang, Wen- Li, and Hsu, David C.
Melt Flow Simulation and Measurement of Extensional Viscosity in
Planar Hyperbolic Dies (243), Olley, P.,Martyn, M.T., Spares, R.,
Groves, D., and Coates, P.D.
|
|
|
|