Representation of a plastic product in a CAE/virtual design environment
requires the measurement of precise quantitative properties on test
specimens exposed to conditions and environments that the product
will see in real life. This kind of testing is different from the
development of 'typical' design properties that one finds in material
databases, and far removed from data found in a materials specification
sheet. 'Typical' properties are measured on virgin or carefully
conditioned materials following carefully defined specifications,
and may not display the influence of the product's real life environment.
For use in design, we might need stress-strain properties of the
plastic after exposure to engine coolant for one application, but
high strain rate properties at low temperature for the same plastic
in another case. While the properties of a metal may not differ
significantly in the examples above, the complex nature of plastics
would result in different measured properties. Failure to observe
and compensate for these differences can result in flawed designs.
Armed with good representative properties however, CAE engineers
can truly analyze product performance. Since it is impractical to
measure all properties under all possible conditions and environments,
a careful evaluation of the specific needs of each class of applications
is needed to keep costs under control. An examination of the real
life environment leads us to an understanding of the kinds of material
properties needed. An expert material testing lab is then able to
select and perform the appropriate tests.
CAE technologies have resulted in greater emphasis being placed
on material testing that elicits quantified measures of plastic
behavior. The cost of durability prove-out will be reduced as fewer
design iterations of a product will need to be tested. While testing
for product development requires significantly greater expertise,
the payoff is useful data that goes beyond the current 'testing
for comparative purposes? and is replaced instead by ?testing to
quantitatively characterize plastic behavior'.
-Hubert Lobo, President, DatapointLabs
ANSYS release aids virtual prototyping
ANSYS 6.0, released in November 2001 empowers engineers and analysts
with a robust design simulation and virtual prototyping solution
to support and streamline the product development process. ANSYS
6.0 has enhanced virtual product simulation capabilities designed
to minimize costs and improve time to market by allowing all necessary
structural, thermal, electromagnetic and fluid-flow design tests
to be conducted within a virtual environment. Product teams can
better determine the real-world behavior of 3-D product designs,
including the effects of multiple physics for added accuracy and
product reliability.
The new ANSYS 6.0 suite features a number of enhancements to provide
engineers the necessary tools to design, test and verify products
under real-world conditions. Usability is key for the end user,
and the ANSYS 6.0 suite offers enhanced functionality. A new Probabilistic
Analysis Method Wizard simplifies the determining process for the
appropriate probabilistic analysis method, and a Shell Section Builder
eases the definition of layered composite elements. Furthermore,
a Variable Viewer that integrates time and history variables into
one comprehensive interface has been added. This addition greatly
simplifies the post-processing of these variables.
ANSYS 6.0 provides an extensive array of nonlinear elements to handle
complex assemblies. The nonlinear capability allows analysis of
stresses, temperatures, displacements and contact pressure distributions
on component and assembly designs.
To enhance solution speed, ANSYS 6.0 added a Symbolic Assembler
- an algorithm with faster ordering - and the introduction of parallel
version of the Sparse solver routines across all computer platforms.
These enhancements to the solver capabilities reduce global matrix
assembly time for the following analysis types: Static, Transient,
Modal, Cyclic Symmetry, Buckling, Harmonic, Spectrum, and Mode Superposition.
-Ann Stanton, ANSYS Inc.
Helmet Impact Simulation Benefits from Foam Material Data
The study of the performance of products and components under impact
conditions is vital to many industry segments ranging from automotive
and aerospace to consumer products and toys. Considerable effort
is devoted to testing of finished products to determine their ability
to meet the challenges they will face in daily life. The objective
of this study was to show how virtual prototyping could help improve
the efficiency of product development by providing answers about
viable designs early in the cycle.
Protective sports equipment is in widespread use in recreational
activities ranging from bicycling to roller blading. The ability
to protect the wearer from injury while remaining lightweight and
comfortable to wear is an important feature of any design. ANSYS/LS-DYNA
was used to simulate head impact when a child rides a bike at 25
miles per hour into a telephone pole. The child's bicycle helmet
was the only barrier between the modeled human skull and the rigid
telephone pole. The helmet, skull and pole were created using standard
CAD tools (Fig. 1). It was meshed using TrueGrid, courtesy of Livermore
Software Technologies, Inc. (LSTC).
The bicycle helmet was made of a cellular energy dissipating foam
covered with plastic membrane or skin. The material properties of
the foam were derived from physical testing of an existing, medium
cost helmet that is typically sold in toy and department stores.
DatapointLabs, an ANSYS Inc. ESP partner, did the testing and produced
material properties that were ANSYS input ready, meaning that the
analyst was able to simply take the data supplied by DatapointLabs,
add it to the geometric and environmental simulation models, and
run the explicit dynamics simulation. The properties were derived
using the following procedures. Cylindrical test specimens were
cut from the foam material. These specimens were then placed between
compressive platens and subjected to compression under impact loads
of 2 and 4 m/s in a Dynatup Instrumented Impact Tower. The resulting
load-time data were converted to load deformation traces, from which,
the stress-strain data were calculated. Compressive data were also
developed using a conventional universal testing machine.
The data were fit to a crushable foam material model, which is capable
of fitting the highly non-linear stress vs. strain response of these
materials. Note the behavior of a typical crushable foam (Fig. 2):
there is a small linear elastic range, followed by a long crush
range, then an exponential increase in stiffness as the foam reaches
its crush limit. A viscoelastic material model was used to simulate
the head response. The density was increased by a factor of 3x in
order to account for the brain matter that was not modeled. The
pole was considered to be a rigid material since it is much stiffer
than the helmet or the head.
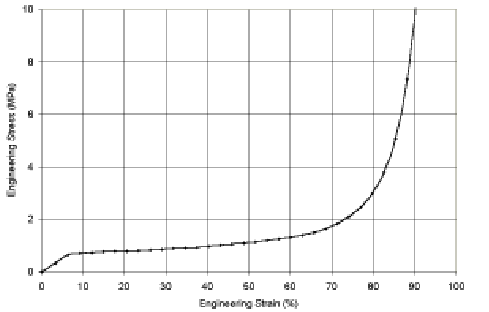
Figure 2. Material data for a
crushable foam
Contact was modeled between the skull and the helmet, the helmet
and the pole, skull and the pole using general node to surface contact
elements. A static friction coefficient of 0.2, dynamic friction
coefficient of 0.1 and a viscous damping coefficient of 10 was used.
For simplicity, the same values were used for all cases. The loading
for the model consisted of an initial velocity of 25 MPH (440 in/s)
forward into the pole (+Z direction), and 6 MPH (105.6 in/s) downward
(-Y direction), applied to both the skull and helmet.
The simulation run time on a single processor NT PC was estimated
to be 30 days. The same problem was run on an SGI with 8 CPU's,
and results were calculated in two hours. The results show that
while the helmet does absorb a significant amount of the energy
of the impact, a high amount of energy is transferred to the skull
and a skull fracture is the predicted outcome (Figs. 3&4). While
model refinement could have some effect on the calculated solution,
the results suggest that a helmet redesign would be needed to dissipate
more of the energy while preventing protective cavity intrusion
by the pole. Alternatively, the helmet could be rated for a lower
impact velocity which would ensure helmet wearer survivability.
-Joe Metrisin and Steve Pilz,
ANSYS Inc.
Our Own Reasons for Studying Bicycle
Helmets
Jamie Antosh, champion BMX cyclist and member of the DatapointLabs
Team, while not testing plastics, satisfies his craving for adventure
in the form of BMX biking. He has been the New York State Champion
for two years in a row and is placed nationally in his class.
Jamie Antosh at the Stars and
Stripes Nationals Race in Pittsburgh.
While Extreme sports certainly illustrate the need for protective
gear, the need and market for this kind of equipment ranges from
the athletic field to the care of the elderly. Material models for
such simulations require rate dependent stress-strain data developed
at high strain rates.
DatapointLabs partners with MSC
DatapointLabs is now a Software Partner of MSC.Software. This partnership
was driven by the needs of our mutual clients: 'Published material
property data is simply not extensive enough to provide the fidelity
that we require in our engineering environment, particularly for
injection molded plastics commonly used in medical products.' says
John Cogger, President, Innova Engineering Inc and MSC.MARC user.
http://www.mscsoftware.com/partners/
More material model options available
Moldflow, in its new 3.0 release now allows users viable, easy-to-implement
options for material modeling. While previous versions relied primarily
on a 2nd order viscosity model and a single PVT and shrink/warp
model, MPI 3.0 shifts to semi-empirical Cross viscosity and Tait
PVT models. However, other models including their classical models
are not excluded. Of greatest interest is the ability to implement
one of three shrinkage models. The choice of which model to use
depends heavily on the material, with simpler models being feasible
for some materials. This may help increase the application of Moldflow
for shrinkage predictions, by reducing the need for the time-consuming
shrinkage characterization as a prerequisite for shrinkage analysis.
DatapointLabs at Moldflow meet
DatapointLabs is a Silver Level sponsor at the rescheduled Moldflow
International User Group Conference. Meet Hubert Lobo and S. Scott
Kumpf at the Sponsor Event.
Upcoming events
SAE 2002 World Congress,
March 4-7, Detroit,MI
Moldflow 2001 International User Group
Conference, March 17-19, Boston, MA
ASTM D20 Committee on Plastics Spring
Meeting, March 10-13, Pittsburgh, PA
2002 ANSYS Users Conference and Exhibition,
April 22-24, Pittsburgh, PA
SPE Annual Technical Conference 2002,
May 5-9, San Francisco, CA
ABAQUS World User?s Conference,
May 29-31, Newport, RI
|
|
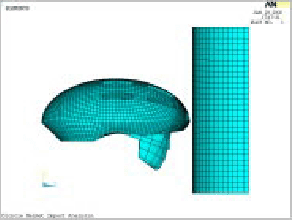
Figure 1. Geometric model of setup
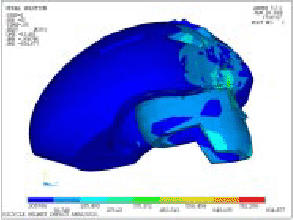
Figure 3. Side view of helmet after impact
Figure
4. Top view of helmet after impact |