For the tensile test case, PLANE183 elements
were used. Again, stresses were compared at 30% strain. Fig. 2 shows
results from simulations using Mooney-Rivlin coefficients generated
using the ANSYS curve-fitting utility, compared to the generic curve-fitting
program. The ANSYS coefficient-based result differs from actual
test results by 10.0% while the results from the generic data analysis
program give a difference of 42.2%.
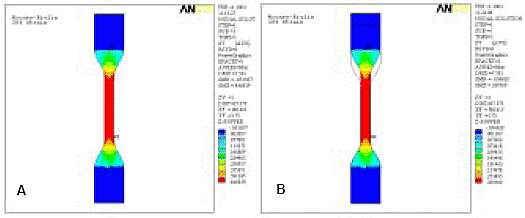
Figure 2. Verification of tensile test
using Mooney-Rivlin coefficients derived by ANSYS (A) and manually
fit with generic curve-fitting programs (B)
Results are based on single runs with one element
type used as well as one strain. The element types selected above
have been designed specifically to be used with the ANSYS curve
fitting program. The quality of the simulation results could depend
on how well the material model fits the test data. Higher node elements
may produce different results. Although there is a great difference
in results much more research must be done in the use of different
elements, materials, loads, and constraints. It must be noted also
that hyperelastic models typically do not fit data well over entire
regions. If the strains seen in the actual application are low,
a model fit in this manner may perform poorly. The proper approach
in this case, is to restrict the range of data submitted to the
regression program so that a better fit is obtained for the region
of interest. Analogously, issues such as precycling or first deformation
(see Datapoint Spring 2001 Issue) must also be considered.
We conclude that for the test case studied, the
ANSYS data-fitting program yielded test parameters that work well
in the ANSYS simulation when used with the appropriate elements.
DatapointLabs has now internalized this methodology so that all
material model parameter development for ANSYS will now be performed
within ANSYS 7.0. A new service is also available to validate the
material models to add an additional dimension of confidence to
the end user. The comparability of the simulation to the actual
experiments performed will be demonstrated.
-Brian Croop and Hubert Lobo
Sourcing Material Data for Virtual Product
Development-Part 1
With global spread of virtual product development
(VPD) and a multitude of modern materials, enterprises are facing
technological challenges in storing, managing and seamlessly exchanging
material property data between interested parties and collaborators.
Our readership represents a diverse cross-section of users of material
properties across automotive OEMs, Tier 1-n suppliers, aerospace,
defense, resin manufacturers and high technology industries. This
article highlights the needs of the VPD community with regard to
“materials issues.”
“We have subscribed to online databases
that boast of properties for >30,000 materials, but we cannot
find the properties we need!” is a common complaint. Online
databases serve as vast collections of simple, comparative material
properties, geared primarily towards providing a material selec
tion tool. They often do not contain the representative 'design
properties' of interest for VPD. Storage and representation of the
complex interdependent behavioral characteristics of materials for
VPD remains a major challenge. No single repository currently handles
such data diversity. Hence, designers within an enterprise utilize
multiple sources of input data, creating the risk of inconsistent
material representation that could adversely affect downstream collaborative
design work. An incorrect representation
of material behavior can be fatal for an involved multi-participant
VPD.
Accordingly, the new need is defined to:
- create a material data management system that
can handle diverse collections of application-specific properties
ranging from simple linear to complex non-linear data
- warehouse quality data from different certified
and identified sources
- provide secure filing cabinets for internal
and proprietary data
- permit easy, but secure exchange of materials
data between collaborators anywhere
- allow data access to be controlled by the ‘data
owner’
- export material model parameters to CAE programs
- include technically competent customer support
for non-linear material models.
Subsets of these needs are satisfied by providers
such as GE Plastics or Moldflow that have introduced plastics databases
containing material properties for VPD. However, these properties
are available to specific constituencies only. They do not offer
broad based interoperability.
The free CAMPUS plastics materials database has
existed for many years. It has acted as a repository of data that
material suppliers do not mind sharing with the public. It is primarily
intended as a material comparator, not a source for design properties.
It does not present VPD communities with a warehousing solution
for the actual materials that they use. It allows output suitable
for limited simulation programs. Matweb is similar in being free
and has similar limitations. Data fidelity and traceability are
issues of concern when designers in enterprises variably use multiple
free databases.
In the “for fee” category, the IDES
plastics material database has assimilated the CAMPUS collection
in addition to its own, along with a search engine to rank and select
materials. However, the data is still comparative and the interface
to design programs, weak. MVision presents a collection of >30
databases with limited connectivity to linear CAE applications.
This results in a vast sea of data so that finding the right data
becomes difficult once again. Further, there is no guarantee that
once the fees are paid the properties of the material of interest
exist within.
While it is clear that a number of options do
currently exist for serving material data, these sources either
lack the depth, breadth or interoperability for this major market.
None of them offer a scaleable, comprehensive and seamless solution
for all the collaborative developmental platforms. They do not provide
tools for control of information that is “enterprise-specific,”
or support the highly sophisticated needs of the VPD community.
-Renu Gandhi.
Next issue - Part 2: a complete solution.
Successful Injection Molding
Beaumont, Nagel and Sherman
Hanser Publications (2002)
ISBN 3-446-19433-9
There has been a long standing need for a book
that describes the process of injection molding using the insights
developed from twenty years of computer aided engineering (CAE).
The authors, all veterans of injection molding CAE, have filled
this need with their book. "Successful Injection Molding"
is a lot more than a book about injection molding CAE. It is clear
at this stage that CAE is a tool, which, if well handled, can provide
excellent results. That being said, a successful implementer of
CAE for injection molding must have a range of insights into the
diverse idiosyncrasies of this enormously complex manufacturing
process. The book is successful in clearly addressing these issues.
CAE has probably done more for the understanding
of the injection molding process than it has for any other application
for which it has been applied. With CAE, a designer can visualize
complex transient events that integrally affect the processability,
shape and performance of the final product being designed. The authors
lead the reader through the molding process as seen through the
eyes of the CAE program, interpreting the observed behaviors along
the way. The book does not stop here, however. Recognizing that
there are still many aspects that cannot be well handled in simulation,
the authors introduces a healthy amount of practical advice on issues
such as the placement of weld lines, flow hesitation and numerous
other factors that can affect part performance. Liberal use of simulation
pictures also help the reader to visualize the phenomena under discussion.
In the Introduction, a methodology is presented
for implementation of a design process that includes CAE, which
helps ensure that all parties involved are clear about their role
in the process. A description of basic polymer behavior and the
injection molding process follows. Chapter 4 gets into design, presenting
part design guidelines. Issues related to the mold design are also
covered including a practical treatment of runner systems, gating
designs and cooling systems. In Chapter 6, CAE is used to understand
the filling process, and the understanding is used to develop design
and process strategies to eliminate flaws in the product. The rest
of the book is devoted to injection molding CAE. The pros and cons
of the different CAE approaches are discussed followed by guidelines
on optimal processes to use when performing simulation. Detailed
chapters on filling, post-filling, mold-cooling and shrink/warp
analysis follow. The book is accompanied by a CD-ROM containing
color figures and computer generated flow animations that are integral
to the understanding of the injection molding process. A spreadsheet
for determining thicknesses for shell surfaces with poor aspect
ratio is also included.
-Hubert Lobo
DatapointLabs to sponsor iMug’03
DatapointLabs will be attending iMUG’03
as a sponsor, April1-3, Pittsburgh. Meet Hubert Lobo and S. Scott
Kumpf at the Sponsor Event.
Upcoming events
SAE 2002 World Congress,
March 3-6, Detroit, MI
Moldflow 2003 iMUG Conference,
April 1-3, Pittsburgh, PA
SPE ANTEC 2003,
May 4-8, Nashville, TN
Fluent Users Group Meeting 2003,
May 5-7, Manchester, NH
ABAQUS User’s Conference,
2003, June 4-6, Munich, Germany
NAFEMS World Congress 2003,
May 27-31, Orlando, FL
NPE 2003,
June 23-27, Chicago, IL
DatapointLabs Has This Fellow...
DatapointLabs President, Hubert Lobo was recognized
as a pioneer for his work in the development of techniques to represent
polymer behavior in CAE by the Society of Plastics Engineers. He
was named “Fellow of the Society” at ANTEC
2002 in San Francisco, last year.
With a strong continued commitment and focus
on meeting material issue needs of the CAE and FEA community, DatapointLabs
makes every effort to be present at our CAE partner events:
iMUG’02, MA
ANSYS User’s Conference 2002,
PA
ABAQUS User’s Conference 2002,
RI
Polyflow UGM 2002,
Belgium
CAD-FEM User’s Meeting,
Germany
AMERIPAM 2002,
MI
We bring back from these events a better understanding of the needs
of the virtual product design community.
DatapointLabs Partners With ESI
DatapointLabs is has signed an MOU with ESI-Group.
The new MOU allows DatapointLabs to develop TestPaks® for ESI software
users.
Look for announcement of availability of these new TestPaks® for
PAM-CRASH and PAMFORM in the coming weeks at www.datapointlabs.com.
Meanwhile, if you have a need, please call our Sales Team 1-888-DATA-4-CAE.
DatapointLabs Deepens Ties With ABAQUS
In a new announcement, the relationship between
DatapointLabs and ABAQUS is strengthened by a new agreement to meet
mutual clients needs. An extensive array of TestPaks®
for ABAQUS can now be viewed directly at the ABAQUS web site TestPaks®
can now be ordered on-line at www.datapointlabs.com.
DatapointLabs will bring the ABAQUS software in-house to facilitate
an enhanced level of support for TestPaks® BOOK REVIEW TM for ABAQUS.
|
|
|